5083船用铝板海水腐蚀速率与阴极保护配套体系研究
在海洋工程领域,铝合金因其优异的比强度、焊接性能和耐蚀性成为船舶制造的重要材料。其中5083铝合金作为典型的Al-Mg系合金,凭借其良好的成形性和中等强度,被广泛应用于船体结构和甲板建造。然而在长期海水浸泡环境下,金属材料的腐蚀问题始终是影响船舶服役寿命的关键因素。本文将从材料科学和腐蚀工程角度,系统分析5083铝板在海水环境中的腐蚀行为特征,并探讨阴极保护技术的配套应用方案。
一、5083铝合金的海洋环境腐蚀机理
5083铝合金的主要成分为镁(4.0-4.9%)、锰(0.4-1.0%)及微量铬,其耐蚀性源于表面形成的致密氧化膜。但在海水环境中,氯离子会破坏这层保护膜,引发以下典型腐蚀形式:
- 点蚀:氯离子选择性攻击氧化膜薄弱区域,形成直径0.1-1mm的蚀坑。实验数据显示,在3.5%NaCl溶液中,5083铝板的点蚀萌生时间约为72小时,蚀坑深度年均增长0.05-0.15mm。
- 晶间腐蚀:镁元素在晶界偏析导致电位差,在盐雾环境下腐蚀速率可达0.03mm/年。
- 电偶腐蚀:当与铜合金等正电性材料接触时,腐蚀速率可能提升3-5倍。
二、海水环境参数对腐蚀速率的影响
通过加速腐蚀试验和实海挂片数据对比,发现腐蚀速率与多重环境因素相关:
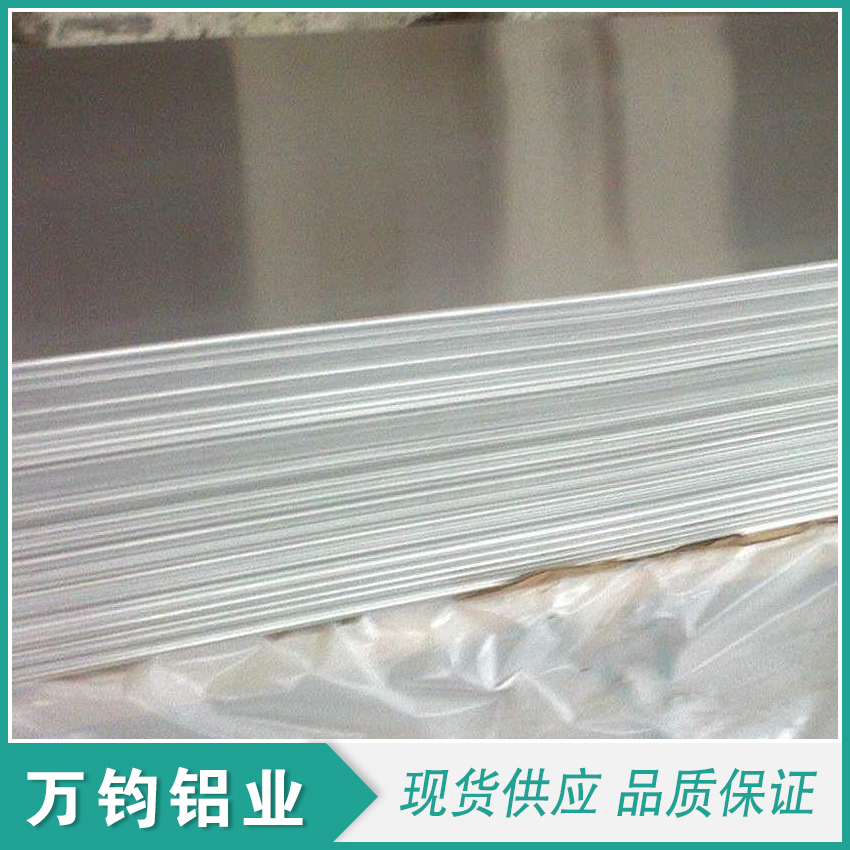
- 盐度:当海水盐度从20‰增至35‰时,腐蚀失重率呈线性增长,斜率约为0.002g/(m²·h·‰)
- 溶解氧:饱和溶氧状态下的腐蚀电流密度比脱氧环境高2-3个数量级
- 温度:Arrhenius方程显示,温度每升高10℃,腐蚀速率增加约30%
- 流速:当流速超过3m/s时,冲刷腐蚀效应导致材料损失率倍增
三、阴极保护配套技术方案
针对5083铝板的特性,工程中常采用混合保护策略:
- 牺牲阳极保护
推荐使用Zn-Al-Cd三元合金阳极,其开路电位-1.05V(vs.Ag/AgCl),与5083铝板(自然电位-0.85V)形成200mV保护电位差。布置密度建议为:
- 船体平坦区域:2.5-3.5kg/m²
- 焊缝及复杂结构处:4-6kg/m²
阳极寿命计算公式:L=W/(I×8760),其中W为阳极质量(kg),I为输出电流(A)
- 外加电流保护
采用IrO2-Ta2O5涂层钛阳极,控制参数包括:
- 保护电位范围:-0.95至-1.10V
- 电流密度:初期50-70mA/m²,稳定后30-40mA/m²
需注意过保护导致的碱性腐蚀,当电位负于-1.15V时可能引发析氢反应
- 涂层协同保护
环氧沥青涂层(干膜厚度250μm)与阴极保护联用可降低电流需求约60%。建议采用:
- 底层:环氧富锌底漆(75μm)
- 中间层:玻璃鳞片环氧(150μm)
- 面层:聚氨酯防污漆(25μm)
四、防护系统优化设计要点
- 电位监测:布置Ag/AgCl参比电极,确保保护电位在-0.90至-1.05V区间
- 电流分布:采用边界元法模拟计算,确保保护电流均匀度>85%
- 维护周期:每6个月检测极化曲线,每2年进行保护效果评估
- 异种金属隔离:采用尼龙垫片或绝缘涂层阻断电偶通路
五、典型案例分析
某型巡逻艇采用5083铝制船体,初始设计未考虑阴极保护,服役3年后出现深度达1.2mm的点蚀。改造方案包括:
- 加装32块Zn-Al-Cd阳极(单重8kg)
- 涂覆改性环氧涂层系统
- 增设4通道电位监控系统
改造后跟踪监测显示,腐蚀速率从0.28mm/年降至0.03mm/年,预计使用寿命延长至25年。
结语
有效的腐蚀防护需要综合材料特性、环境因素和工程技术。对于5083船用铝板,建议采用"涂层+牺牲阳极+监控系统"的三重防护体系,通过定期检测和维护,可将年腐蚀速率控制在0.05mm以下。随着新型Al-Mg-Sc合金和智能阴极保护系统的发展,未来船舶铝合金的防护将向更高效、更智能的方向演进。